發(fā)帖
評論
新能源電機測試解決方案:電機試驗平臺的創(chuàng)新實踐
電機試驗平臺作為電機研發(fā)、測試和性能驗證的重要工具,其設(shè)計與應(yīng)用直接關(guān)系到電機產(chǎn)品的質(zhì)量控制和性能優(yōu)化。隨著工業(yè)自動化、新能源汽車等領(lǐng)域的快速發(fā)展,對電機性能的要求日益提高,電機試驗平臺的設(shè)計也呈現(xiàn)出智能化、高精度和模塊化的趨勢。以下從設(shè)計要點、關(guān)鍵技術(shù)、應(yīng)用場景及未來發(fā)展方向展開分析。 一、電機試驗平臺的設(shè)計要點 1.系統(tǒng)架構(gòu)設(shè)計 電機試驗平臺通常由機械加載系統(tǒng)、電氣測控系統(tǒng)、數(shù)據(jù)采集與分析系統(tǒng)三大部分組成。 機械加載系統(tǒng):包括負(fù)載模擬裝置(如磁粉制動器、伺服電機對拖等)、機械傳動機構(gòu)(聯(lián)軸器、扭矩傳感器)和支撐結(jié)構(gòu)。設(shè)計時需考慮負(fù)載的動態(tài)響應(yīng)特性,例如新能源汽車電機測試需模擬復(fù)雜路況下的瞬態(tài)負(fù)載變化。 電氣測控系統(tǒng):核心是功率分析儀、變頻器和PLC,用于控制電機的輸入電壓、電流和頻率,并實時監(jiān)測輸出參數(shù)(如轉(zhuǎn)速、扭矩、效率)。 數(shù)據(jù)采集系統(tǒng):通過高精度傳感器(如霍爾傳感器、編碼器)等軟件平臺實現(xiàn)數(shù)據(jù)可視化與分析,支持生成效率MAP圖、溫升曲線等關(guān)鍵報告。 2.關(guān)鍵參數(shù)與精度要求 測試范圍需覆蓋電機的全工況,例如低速大扭矩(電動汽車驅(qū)動電機)或高速超(機床主軸電機)。 扭矩測量精度通常要求±0.1%FS(滿量程),轉(zhuǎn)速控制精度需達到±1RPM以內(nèi)。 動態(tài)響應(yīng)能力是難點,例如伺服電機測試需實現(xiàn)毫秒級的負(fù)載階躍響應(yīng)。 3.安全性與可靠性設(shè)計 過流、過溫、振動超標(biāo)等多重保護機制必不可少,例如通過硬件急停電路與軟件閾值聯(lián)動。 電磁兼容(EMC)設(shè)計可參考國際標(biāo)準(zhǔn)(如ISO7637),避免高頻開關(guān)器件對測試信號的干擾。 二、核心技術(shù)突破方向 1.實時仿真與數(shù)字孿生技術(shù) 現(xiàn)代試驗平臺正逐步數(shù)字孿生技術(shù),通過RTLAB等實時仿真系統(tǒng)構(gòu)建虛擬電機模型,與實際測試數(shù)據(jù)閉環(huán)校驗。 2.AI驅(qū)動的測試優(yōu)化 機器學(xué)習(xí)算法可用于自動識別測試異常(如軸承磨損導(dǎo)致的諧波畸變),并動態(tài)調(diào)整測試策略。某企業(yè)采用學(xué)習(xí)分析電機振動頻譜,將故障診斷準(zhǔn)確率提升至98%。 3.高動態(tài)負(fù)載模擬技術(shù) 針對高速電機測試,飛輪儲能或電渦流加載裝置可模擬瞬態(tài)沖擊負(fù)載。某型號直升機尾槳電機測試平臺采用磁懸浮軸承技術(shù),實現(xiàn)了20000RPM下的無接觸加載。 電機試驗平臺的設(shè)計已從單一性能測試轉(zhuǎn)向全生命周期驗證,其技術(shù)演進將持續(xù)推動電機產(chǎn)業(yè)向智能化邁進。未來隨著寬禁帶半導(dǎo)體器件的普及,測試平臺還需適應(yīng)更高開關(guān)頻率與更嚴(yán)苛的EMC挑戰(zhàn),這既是技術(shù)難點也是創(chuàng)新的突破口。
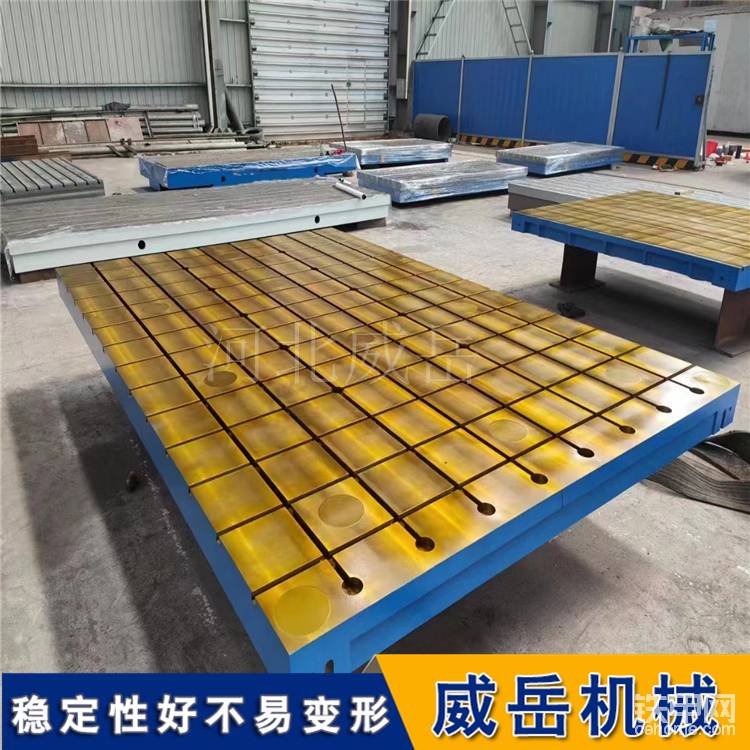
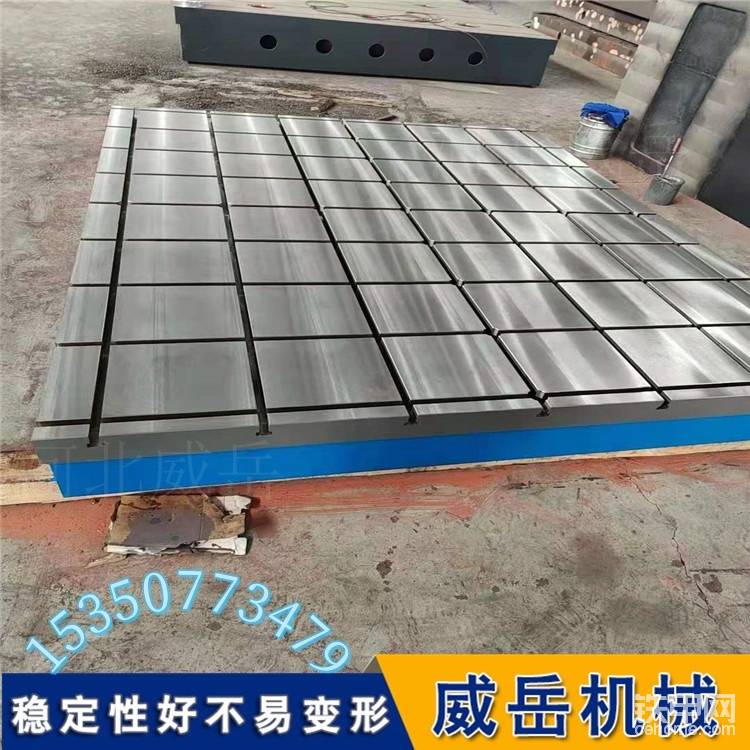
圖片